WHAT IS WORK ACCIDENT?
According to Article 11/A of the SSK Law, it is an event that occurs in one of the following situations and causes the insured to malfunction in body and spirit immediately or afterwards. While the insured is at work, the insured is transported to and from the place where the work is done in a vehicle provided by the employer, at the time allotted to give milk to the child of the lactating woman insured, due to the employer being sent to another place on duty due to work carried out by the employer.
Occupational Health and Safety according to TS 18001; conditions and factors that affect or are likely to affect the health and safety of employees or other workers, visitors and other people in the workplace.
WHAT ARE THE BENEFITS OF THE TS 18001 OCCUPATIONAL HEALTH AND SAFETY MANAGEMENT SYSTEM?
It provides the improvement of employees and society by reducing diseases and disabilities. It provides added value and money savings with efficient allocation of resources. It ensures that possible dangers that may result in damage are determined in advance and necessary precautions are taken.
Employees are protected from the negative effects of the workplace, and they are provided to work in a comfortable and safe environment. Employee satisfaction, customer satisfaction and reduction in production costs are ensured. Extremely high costs of work accidents and occupational diseases are minimized
COSTS OF ACCIDENTS
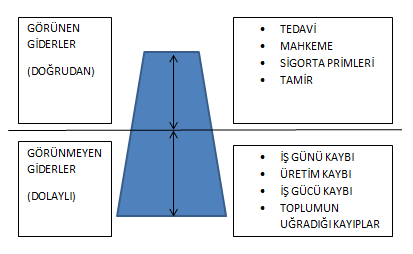
WHAT ARE THE EFFECTS OF OCCUPATIONAL ACCIDENTS?
- SOCIOLOGICAL
- PSYCHOLOGICAL
- MEDICAL
- ECONOMIC
In terms of the employee; may be in the form of injury or death.
In terms of employer; production and productivity are adversely affected.
In terms of the country's economy; The social security system is damaged, the country's resources are wasted and national welfare is negatively affected.
WHAT ARE THE FACTORS AFFECTING HEALTH?
1. PERSONAL FACTORS: Eating habits and cleaning habits
2. ENVIRONMENT: Physical Environment (hot, cold, ventilation)
3. Biological Environment (agriculture, livestock, bacteria, microorganisms)
4. Social Environment (traditions, culture, beliefs)
5. Psychological Environment (inattentiveness, nervousness, apathy, inattention)
6. OTHER FACTORS: Hereditary
DEFINITIONS AND RECIPES
Acceptable Risk : Reduced risk to a level that the organization can tolerate in accordance with legal requirements and its own OHS policy.
Examination: A systematic, independent and documented process for obtaining and objectively evaluating "audit evidence" to determine the degree to which "audit criteria" are met.
Danger : A source, situation, or action that could result in injury or ill-health, or a combination of these.
Event : Work-related events that cause or have the potential to cause injury or ill health or death.
Occupational health and Safety : Conditions and factors that affect or are likely to affect the health and safety of employees or other workers, visitors and other people in the workplace.
Occupational Health and Safety Management System: Part of the entire organization's management system used to develop and implement the organization's OH&S policy and manage OH&S risks.
Risk : The combination of the probability of a hazardous event or exposure occurring and the severity of the injury or ill health that the event or exposure may cause.
HOW IS THE OCCUPATIONAL HEALTH AND SAFETY MANAGEMENT SYSTEM ESTABLISHED?
1. PLANNING PHASE: All goals and objectives of the organization are determined, implementation methods are developed.
2. ACTIVITY PHASE: The plan is implemented and the agreed measures are taken in line with the objectives of the organization.
3. EVALUATION PHASE: The activities within the plan are checked for effectiveness and adequacy, and the results are compared with the plan.
4. CORRECTIVE ACTION PHASE: Identified deficiencies are eliminated, the plan can be revised according to changing conditions, and the procedures are restructured as necessary.
WHAT ARE THE OCCUPATIONAL HEALTH AND SAFETY MANAGEMENT SYSTEM REQUIREMENTS?
1. GENERAL CONDITIONS
2. OCCUPATIONAL HEALTH AND SAFETY POLICY
3. PLANNING
4. APPLICATION AND OPERATION
5. CONTROL
6. MANAGEMENT REVIEW
1. GENERAL CONDITIONS
The organization shall establish, document, maintain and continually improve an OH&S management system in accordance with the requirements of this OH&S standard and determine how the OH&S management system will meet these requirements.
The organization should describe and document the scope of its OSH management system.
2. OCCUPATIONAL HEALTH AND SAFETY POLICY
The OHS policy should ensure the following: It should be appropriate to the nature and magnitude of the organization's OH&S risks. A framework for setting and reviewing OSH targets should include a commitment to prevent injuries and ill health and to continually improve OSH management and OHS performance. It must be documented, implemented and maintained. It should be announced to all employees under the control of the organization so that employees are aware of their individual OHS responsibilities. It should be accessible to interested parties. It should be reviewed periodically to ensure that the organization remains relevant and relevant to it.
Topics that can be covered in the OHS policy; reducing accidents, safe working environment, reducing risks, training and participation of employees, importance given to healthcare professionals, compliance with laws, continuous improvement.
3. PLANNING
a) Hazard Identification, Risk Assessment and Determination of Controls
The organization should establish and maintain procedures to identify hazards, assess risks, and identify necessary controls on an ongoing basis.
Risk assessment should be preventive rather than corrective and is divided into two as corrective and preventive.
In the corrective risk assessment, it is envisaged that the risk assessment will be carried out and control measures will be initiated after the activities and procedures have been established and the changes implemented.
In the preventive risk assessment, it is envisaged that the risk assessment should be made and measures should be taken before the changes and activities are implemented.
Eliminating the risk is the basic principle in the control measures that can be taken, if the risk cannot be eliminated, it should be reduced and protective equipment should be used at the next stage.
The control methods that can be taken are divided into 3; Engineering Control: Equipment and facility design, creating a process that eliminates hazards.
Administrative Control: Procedure, instruction, etc. creating documents, giving work permit, limiting working time, warning sign, training.
Personal Protective Equipment: Gloves, headgear, earmuffs, work clothes
Operational activities are divided into 5 parts; Continuous Works: Production, Painting Infrequently Done Jobs: Maintenance, Cleaning, Heavy and Dangerous Works, Things Done Inside the Company Site, Things Done Outside Chemical, Mechanical, Biological, Electrical Activities
The hazard classes are below; Dangers Caused by Gravity
Falling from height, falling into a pit, falling pieces, slipping, stumbling, tripping Burn-Scald
Flame combustion, hot surfaces, hot liquids, steam Fire-Explosion
Combustible gas, steam, natural gas, LPG, flammable liquid, flammable solids, flammable dusts, flammable chemicals, cigarettesEnvironmental and Natural Hazards
Earthquake,flood,storm,lightning,snow,extreme heat/cold Pressure Systems
Compressed gases, compressed air, vacuumMachine-Equipment Hazards
Moving parts, getting caught in rotating equipment, sharp edges, flying, shattering, splintering partsElectrical Hazard
High voltage, damaged cables and sockets, overloaded circuits, unsuitable panels
Transport-Lifting Vehicle Hazards
Electrical Hazard
Overloading of cranes, forklifts and pallet trucks, vehicle traffic, elevators
Biological Hazards
Laboratory work, food-borne diseases, blood-borne diseases Chemical Hazards
Carcinogenic, corrosive, corrosive, irritant, toxic Ergonomic Hazards
Forced positions, repetitive movements, prolonged static positionsTransportation HazardsRadiation Hazard
b) Legal and Other Terms
The organization should be aware of how the relevant legal and other requirements affect its activities or how they will affect it in the future and should communicate this information to the relevant personnel.
Some Turkish Labor Legislations are below;
- Business rules
- SSK Law
- Occupational Health and Safety Regulation
- Machinery Safety Regulation
- Regulation on the Transport of Dangerous Goods by Land
- Hazardous Chemicals Regulation
- Noise Control Regulation
- Grounding Regulation in Electrical Installations
c) Goals and Programs
The organization should try to achieve its OHS policy and objectives by establishing an OHS program. For this, strategies and trading plans need to be developed. These strategies and trading plans should be documented and published. Progress towards achieving OHS targets should be monitored, reviewed and recorded. Accordingly, strategies and trading plans should be updated or changed as necessary.
The organization shall establish, implement and maintain documented occupational health and safety objectives at each relevant function and level within it.
Targets should be expressed in measurable quantities where practical and consistent with the OSH policy.
Goals should be set to ensure continuous improvement.
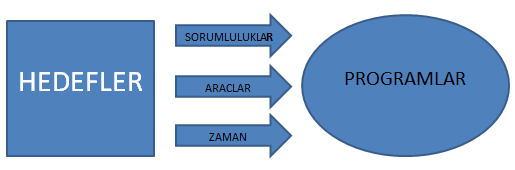
4. APPLICATION AND OPERATION
a) Resources, Duties, Responsibility, Accountability and Authority

b) Education, Awareness and Competence
The organization should ensure that personnel performing tasks in the workplace that may affect OHS under its control are competent in terms of appropriate education, training or experience, and should maintain relevant records.
The organization should identify the need for training regarding OH&S risks and its OH&S management system. The organization should provide trainings or take measures to meet this need, evaluate the effectiveness of the training or measure taken, and keep the relevant records.
There are 3 types of training;
Training for All Employees: First Aid, Fire Protection and Prevention, Safe Use of Liquid Chemicals and Gases
System-Oriented Trainings: Accident Assessment Hazardous and Harmful Substances ManagementWarning Signs Stakeholder Information
Job-Specific Trainings: General Occupational Safety Manual Load Lifting TechniquesNatural Gas Crane Signing Adaptation TrainingsIn-Unit Training System Manuals
c) Communication, Participation and Consultation
The organization establishes, implements, and maintains procedures regarding OH&S hazards and its OH&S management system;
The organization should encourage all those affected by its work to participate in OSH practices and support its OHS policy and OHS objectives through a consultation and communication process.
d) Documentation and Document Control
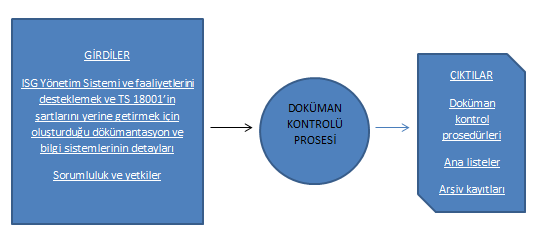
e) Business Control
The organization shall establish and maintain arrangements to ensure the effective application of controls and countermeasures where necessary to control operational risks, implement OSH policy, achieve OSH objectives, and comply with legal and other requirements.
f) Emergency Preparedness and What to Do in Such Situations
The organization should identify potential emergencies and be able to ensure that necessary action is taken in such emergencies.
Emergency plans should be as follows; Definition of the emergency situation Description of the personnel to take charge Responsibilities and authorities of the personnel to be assigned What will happen to the dangerous materials in an emergency Internal and external communication Protection of vital equipment Emergency equipment Evacuation of the emergency scene
Emergency equipment includes;Alarm systemsEmergency lighting and powerEscape routesAssembly pointsShelterCritical isolation valves,switches and breakersFire equipmentFirst aid suppliesCommunication tools
Drills should be scheduled, outside help should be encouraged, emergency plans should be tested, malfunctions should be detected, emergency equipment should be checked.
5. CONTROL
a) Performance Measurement and Monitoring
b) Evaluation of Conformity
c) Accidents, Incidents, Nonconformities, Corrective and Preventive Actions
6. MANAGEMENT REVIEW
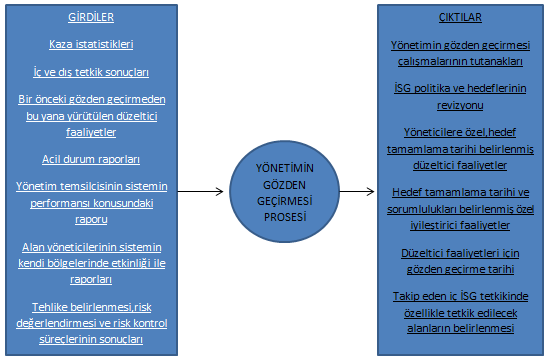